远离车身制造信息孤岛:数字化转型三大原则
车身制造必须速度更快、成本更低,材料更新。
汽车制造现在正面临着来自时间、质量和成本三方面的压力。现阶段的汽车制造需要在生产过程中快速掌握铝制件和高强钢等新型材料,并且在短时间内向市场交付创新且高质量的电动车型,同时还要满足消费者对于鲜明的功能以及独特设计的新需求等等。
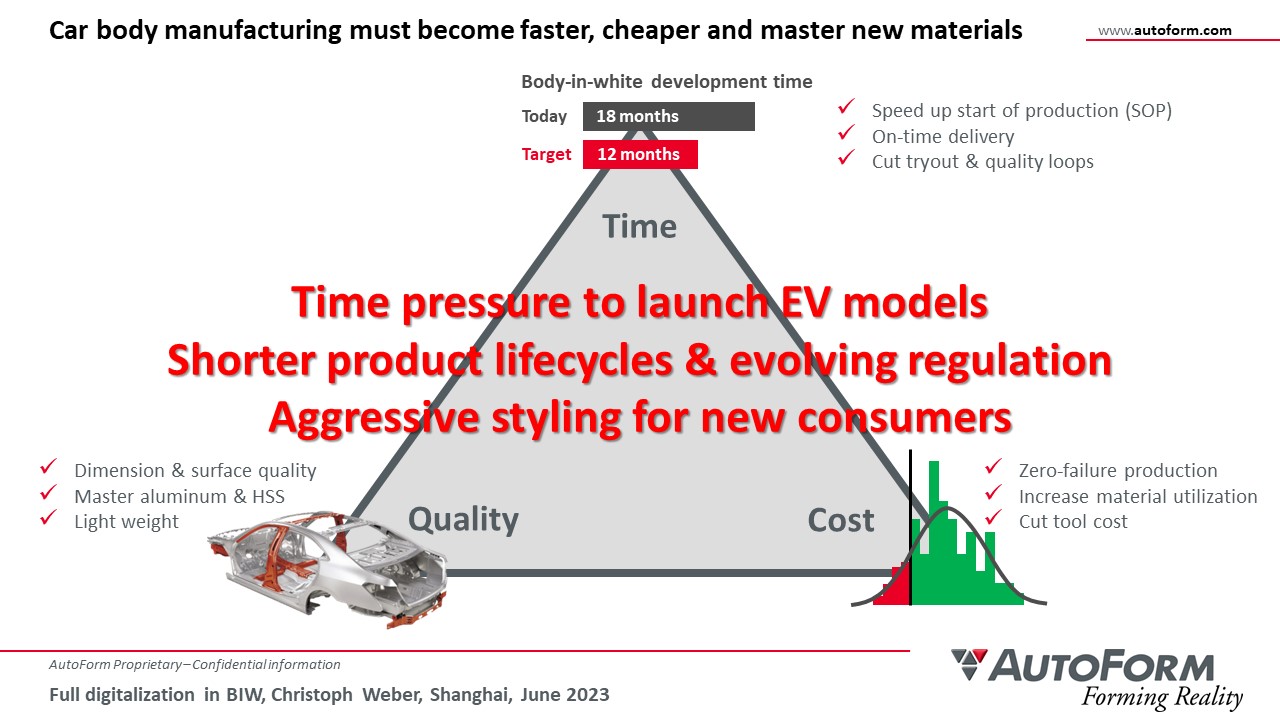
图源:嘉宾演讲材料
在车身制造数字化的过程中,AutoForm软件可以帮助一个典型的主机厂将SOP(标准作业流程)时间缩短6个月,并且做到每年节省2亿元以上。通过前期运营环节的投入,优化制造环节,从而降低制造时间和成本。
打破信息孤岛
现阶段车身制造存在的问题就是,在开发过程中,各个部门都会在内部进行自我优化,但是整个开发系统彼此之间的优化却容易被忽略。比如说,在设计环节,设计部门设计出良好的冲压、焊接和装配流程,但是由于各环节之间的信息孤岛,导致这些流程无法完全转达到供应链进行执行,其中的一些经验和信息被忽视和消耗,导致部门和部门、主机厂和供应商之间存在信息差,使得一些本该解决的问题悬而未决。
所以在开发新车型、新车身和白车身的同时,无论是技术团队还是咨询团队,甚至是供应商之间都需要共同努力,建立协同合作,打破各个环节之间的信息孤岛。在优化自身环节的同时,做到整个系统共同优化。
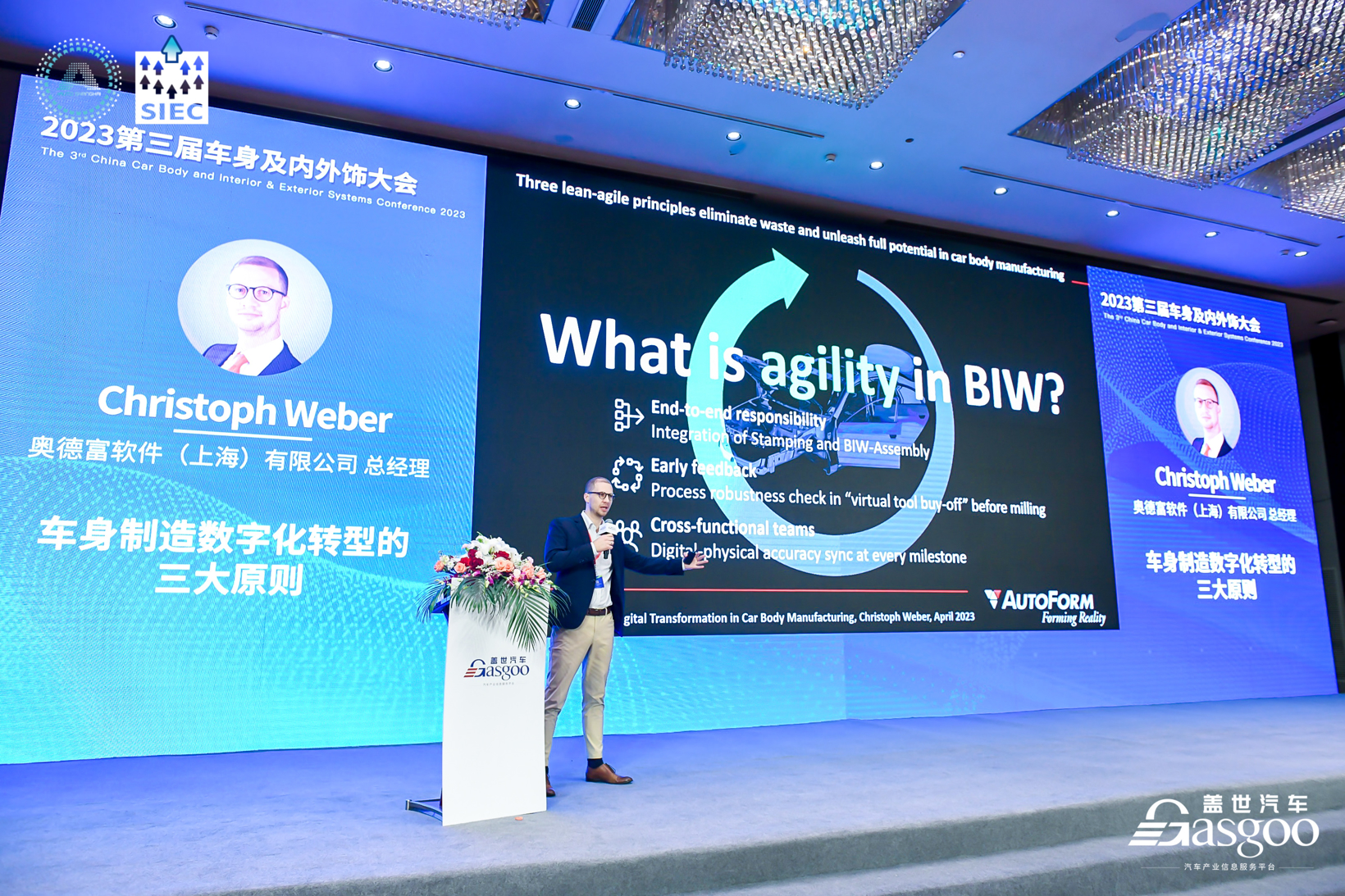
为此,奥德富软件(上海)有限公司总经理Christoph Weber在2023第三届车身及内外师大会上表示,车身制造数字化转型需要做到以下三大原则,来让开发和制造环节变得更加灵活。
第一,点对点负责。整合冲压车身和白车身的装配,实现冲压与白车身组装一体化,进而实现整体系统的优化。
第二,基于工作系统优化各项环节。在虚拟世界里优化成本并降低风险,协助用户优化价值。
第三,跨职能团队。对每个环节都进行准确性的检查,将制造车间和其他各部门联系到一起。
车身制造数字化三大原则
我们以德国某著名主机厂为例,具体阐述点对点的好处。当我们遇到总成精度超差时,传统的方式是想通过优化单件,将单件优化至尽可能接近理论状态以提高总成精度。但是单件优化并不能保证得到最好的装配结果,在装配过程中,仍然可能会遇到意料之外的变形。虽然通过试错环节改变某个单件的尺寸能得到更好的装配结果,但是单件的重新调整已经导致了前期的过工艺和浪费。
现在,我们不再对单个零件进行局部优化后再进行装配,而是将其放到AutoForm Assembly中,对整个总成进行评估。从总成的组建和装配开始,通过多次仿真,当发现内部需要预变形某些单件才能达到总成精度要求时,则按照新的单件要求进行精确制造,最终获得满意的装配结果。AutoForm通过这种点对点的责任,在其他行李箱装配、热成形装配等等环节,做到了将SOP时间缩短6个月。
其次是基于工作系统优化各项环节。供应商可以通过模拟仿真来预测可行性和进行最终工艺验证,在实际生产之前解决问题。
但仍然会遇到某个部门环节或者某个过程设计,在电脑上进行仿真的时候没有发现问题,但是实际制造的过程中却出现开裂、起皱、回弹等等问题的情况。
评论区域